Le Groupe Richemont, en me confiant une direction de production, souhaitait diminuer les délais de livraison, améliorer la production et diminuer ses coûts pour l’une de ses manufactures de haute horlogerie.
Quand on additionne tous les temps pour former, usiner, polir, assembler et contrôler les pièces d’une montre, la durée totale est assez courte. En regardant de près toutes les étapes, j’ai constaté qu’un certain nombre d’entre elles ne créaient pas de Valeur Ajoutée – au sens où la Valeur Ajoutée est ce pour quoi le client est prêt à payer. Dans le cas de l’horlogerie, ce sont typiquement les opérations de regroupement en lots, stockage, déplacement, conditionnement pour ces mêmes déplacements, nettoyage au retour du stock, etc. En fait, chaque geste ou utilisation de machine, d’outils, d’énergie et de temps qui ne transforme pas avantageusement de la matière ou des composants vers le produit fini n’est pas Valeur ajoutée.
C’est un peu comme si vous cuisiniez des ingrédients séparément, puis que vous les congeliez, avant de les réchauffer à nouveau pour ensuite les intégrer dans votre recette finale. Chauffer, congeler, décongeler et réchauffer ne sont pas des opérations à Valeur Ajoutée. Transporter, stocker puis nettoyer des pièces d’horlogerie n’ajoute aucune valeur à la production d’une montre, qu’elle soit de luxe ou non.
L’évaluation de chaque opération, l’observation des moindres actions et le calcul de l’ensemble des déplacements des pièces m’ont permis de dresser une carte de l’usine avec les distances parcourues et le temps passé à attendre, à faire du travail avec Valeur Ajoutée et du travail sans Valeur Ajoutée.
Par exemple, pour le mouvement d’une montre de quelques centimètres de diamètre et pesant quelques grammes, les composants ne parcouraient pas moins de 900 km.
L’ouverture au changement
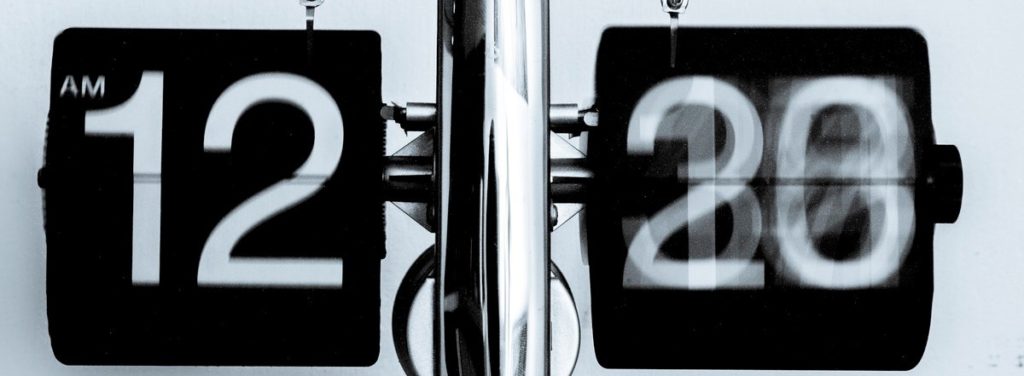
S’il faut réellement une à quatre heures pour réaliser toutes les opérations d’une montre, il doit être possible de caser sa production complète en dix jours. Mais pour réussir ce tour de force et passer de la théorie à la réalité, il fallait que les collaborateurs soient ouverts aux propositions de changement que j’allais leur faire.
C’est en travaillant sur le terrain avec les équipes de production, mais surtout en repérant et mobilisant les agents de changements de l’entreprise, que j’ai pu proposer des actions concrètes pour que chaque moment passé sur la production des montres ajoute de la valeur au produit fini. Si, par exemple, l’immobilisation du produit en cours de fabrication n’était pas utile, on décidait de supprimer ce temps d’attente.
En remettant en question l’organisation, la manufacture a maximisé l’utilité du temps et augmenté la performance. Rien n’a été changé dans les techniques et métiers horlogers. Les équipes ont continué de polir, de découper et de souder. On a plutôt changé la disposition physique des postes de travail et des machines et surtout l’organisation temporelle.
Le secret de l’excellence est dans le délai court
Quand on n’a pas le temps, on ne fait que ce qui est utile. C’est ce qui se passe quand on raccourcit les délais de production.
Le résultat a été fulgurant. En l’espace de cinq mois, nos délais sont passés de dix mois à neuf jours trois quart.
En enlevant les temps d’attente et les opérations inutiles, on a réussi à diminuer les délais, les stocks, des dizaines d’opérations finalement inutiles et, de ce fait, 30 % des coûts marginaux.
Quant à la qualité des produits, nous l’avons abordée sous l’angle des conséquences de la non-qualité : ça coûte ! En identifiant et en ciblant spécifiquement les causes des coûts de la non-qualité, nous avons divisé par 5 ces coûts.
Travailler à délai court ne réduit pas seulement les coûts, cela permet aussi de réduire les impacts d’une erreur ou d’une imperfection.
Réduire les stocks et les risques. Augmenter les bénéfices.
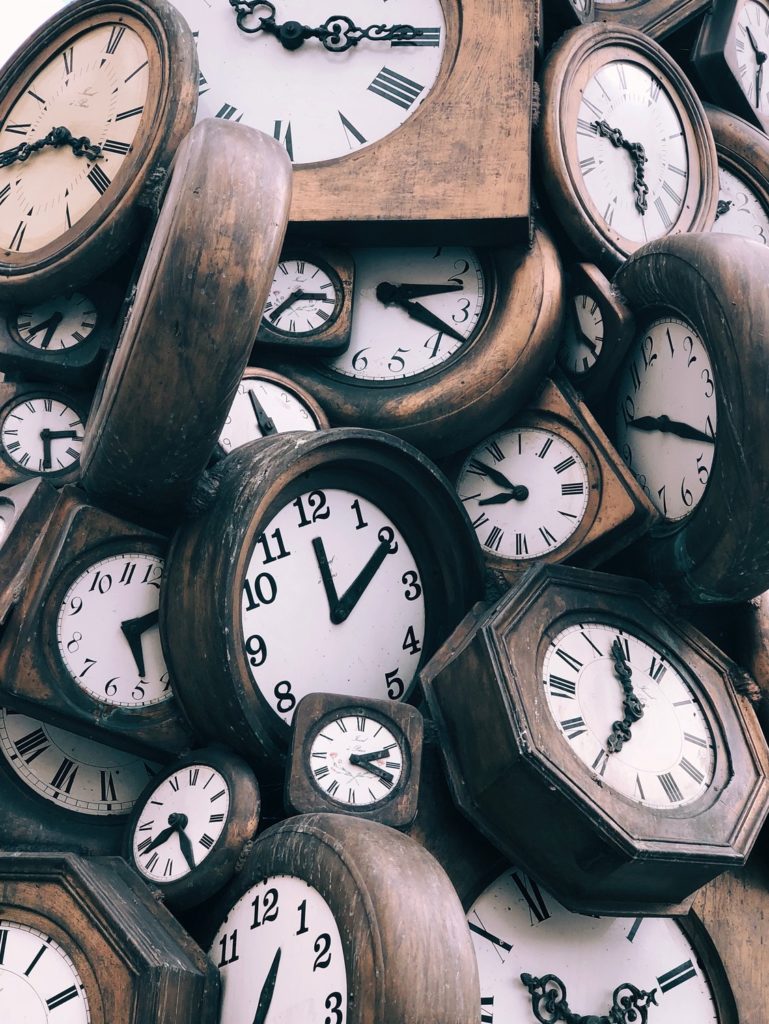
La manufacture en question produit aujourd’hui des montres en 7 jours, dont 5 sont exigés par des normes de contrôle de bonne marche. Dans les faits, l’équipe de cette manufacture a réduit sa production à deux jours de travail entre la commande et la finition. Son ambition est de produire les montres sur commande, dès qu’une est vendue quelque part dans le monde.
Ce qui était révolutionnaire il y a dix-huit ans continue de l’être aujourd’hui. Cette manufacture de la marque Cartier continue de progresser selon notre approche.
Comment l’excellence opérationnelle peut-elle être déployée dans les infrastructures de distribution d’énergie ?
Dans un prochain article, j’expliquerai comment, en faisant moins, on peut parfois en faire plus.

